Rosa Gres Sustainability: Project Zero
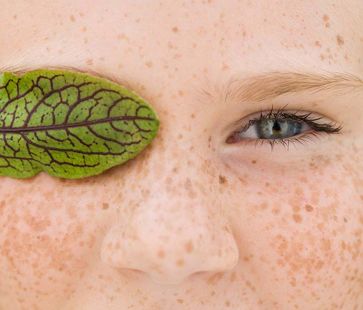
Since 2010, Project Zero encompasses Rosa Gres’s compromise regarding environmental sustainability, which is implicit in our philosophy of Corporate Social Responsibility. The main ideas of Project Zero are:
To continuously improve in a transversal manner that affects the whole company, while aware of both the short-term and long-term future.
To produce in an efficient and controlled manner, in order to reduce the consumption of natural resources.
To not generate residues during the production process: separate, reuse, assess.
To foresee and control the environmental impact of the finished Rosa Gres product: its transportation from the factory, its useful life and its final recycling.
Water Management: this is how we reuse 100% of our water
By using our purification system we reuse 100% of the water of the productive process. We have designed a complete, closed and completely sustainable circuit that works in 3 basic phases:
- We separate the water from the mud with a physical and chemical treatment.
- The mud is reintroduced into the ceramic paste.
- 100% of the clean and purified water is returned to the production process.
With this system we save up every year 11,000 m3 of water, the equivalent of filling up to 730 pools a year.
Natural and Energetic Resource Control
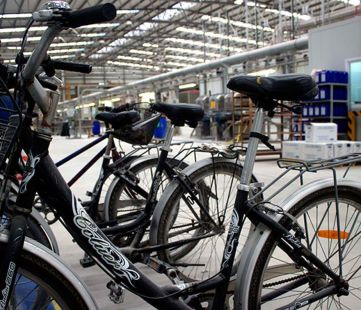
We use an online control system to manage the consumption of energetic resources, water and CO2 emissions. These are some of our important milestones:
> 22% less CO2 emissions
> 20% less general energetic consumption
> 26% less natural gas consumption
We review the source of the necessary energetic resources for the production process and continuously optimize it.
We obtain 100% of our electric energy from renewable sources. We generate warm water with solar power.
Comprehensive Recycling Program
We apply a recycling program to the entirety of the ceramics production cycle:
- We recycle 100% of the rubble generated by the production process.
- We grind the dry rubble in a mill used only for this purpose (Gruber) and then reintroduce it into the paste. Thus we eliminate the residue and avoid its transportation.
We assess the cooked rubble to transform it into the sub-base of roads or raw ceramic material.
Residue Management: 100% recoverable
- At our factory in Vallmoll we count with 30 perfectly identified residue control and pick-up points.
- Each residue is segregated and stored in a differentiated way.
- We count with 24 different residue classifications.
We assess all residues via authorized companies to turn them into sub-products.
Rosa Gres collaborated in designing the DAPc®
We were part of the committee that designed the DAPc® system for ceramics, the first type III Eco tag created in Europe. During the project, 4 phases of the lifecycle of ceramics were analyzed. It was a unique and pioneering experience.
The project was carried out in collaboration with the Environmental Management Investigation Group (GIGA) of the ESCI School of International Commerce (UPF, Barcelona) and the Ceramic Technology Institute (ITC) of the Jaume I University of Castellón.
The DAPc eco tag is in force in Europe since 2009 and all Rosa Gres products are certified with it.
Eco-design is our working system
When we project a product, we calculate the environmental impact that it could generate throughout its lifecycle, and then reduce it to a minimum. In each phase we study and perform:
- Design. Selection and analysis of raw materials, inks and varnishes. We avoid materials that contain heavy metals.
- Shopping management. We base our work on the Km Zero philosophy to decide where to perform our purchases and thus reduce transportation requirements and the emissions that go with it. We review the environmental management of our suppliers.
- Manufacturing. Packaging without white paper.
Final transportation, use, maintenance and deconstruction.
The factory: built sustainably
The Rosa Gres factory in Vallmoll was constructed in accordance with the principles sustainable construction. The facilities are considered IBE, which stands for Low Emission Facilities.
The plant counts with natural ventilation. The temperature remains stable throughout the year. This is thanks to a system of mobile panels, installed on the sides of the walls.
The roof was designed by creating a structure of skylights that let in a lot of sunlight. This way we save energy and the atmosphere is more comfortable.
The factory counts with a total surface of 32,000 m2. We use bicycles to move around the facilities.
The aim of Rosa Gres is to continuously improve the work environment.